611 High Street
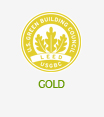
Project was selected to be the 1st project on campus to be completed with the intension of attaining a LEED Silver Level Certification. On completion the team attained a LEED-CI Gold Level Certification.
Miller, Miller & McLachlan was contracted by Lafayette College at the conception of the project to be their Construction Manager along with Studio ABK Architects of New Haven Connecticut as the Design Team.
Due to the extensive repairs required we set the construction time at 12 months.
Schematic specifications were received August 2010. Two budgets were generated before putting this out to bid
Board of Trustees Approval was granted in spring. A Pre-Bid walk through was completed on 5/17/11 with subcontractors and suppliers. Bids were received and the GMP Proposal submitted to the College by June 8, 2011. This was discussed and adjusted again on 6/24/11. The original Bid had (25) Alternates. This allowed the College wide latitude to fine tune the final project scope.
A May 16, 2012 Deadline was set for project completion by the College. This was supposed to allow time for commissioning and the installation of furniture before the student return in the middle of August.
Contracts were signed on 7/15/11 and demolition started in the week of 7/20/11. Like most renovations of older buildings the real challenges begin after unknown elements are exposed.
It was found that this building had been rebuilt after a fire. A number of the structural wood elements were badly burnt, but still in place. These structural members along with charred floor boards were removed and replaced.
Originally this building had a grand entry with a large stairway to the 2nd floor. After the fire when the building was renovated a new stair system was introduced to the 2nd & 3rd floors. The exterior windows on the north side of the building that originally lined up with the main stair landing no longer lined up. One window was in the stair well and the other was in a room with half the window above the floor and half below.
Needless to say these windows did not line up with the new design and stairwell layout. One of our many challenges was to remove the two north side dormers and rebuild them at an elevation that was coordinated with the current design. This of course had to be completed in a way that left the building appearing as if the adjustment was never made.
Construction was allowed to start with the extensive demolition package even before the Building Permit was received. Demolition and any work that did not require City of Easton inspection continued, while the 3rd Party review process tied up the release of the Building Permit.
Differences on Code interpretation were settled and the permit was received. These differences resulted in Addendum #1. This document included (22) written pages along with (28) drawings.
Our overall goal was to completely renovate this Neo Georgian building, giving it a serviceable life of 20-30 years. To satisfy the Donor and the College this had to be completed in a way that would leave the building’s exterior appearance unchanged while recreating a unique décor on the interior.
This 3.2 Million-Dollar renovation resulted in the transformation of the 11,554 SF Phi Gamma Delta Fraternity into the Grossman House, a dynamic 21st century building with state of the art mechanical, electrical and communications systems. This transformation changed this from a fraternity to dwelling type units. Many innovations were designed to meet the LEED goals. This included a rain water recovery system. This system collects rainwater and reuses it to flush toilets. We adjusted the design to include a solenoid valve that would allow the toilets to function off the domestic water if the water level in the tank was too low or during a power outage.
The Structure was totally gutted. Wood floors and wood structure had to be removed on each floor to allow the installation of new structural elements. To satisfy LEED requirements all materials removed from the building were weighed before they were sent to recycling or put in a dumpster.
We logged 832,187 LBS of materials and equipment removed from the building. 592,475 LBS of the material and equipment was recycled. This is 71.2% of the total material.
Our onsite information was very accurate. Final weigh slips at the transfer station showed an additional 19,448 LBS of waste. We determined this was due to rain that was absorbed in the open dumpsters.
During the demolition we discovered that the 3rd floor had short parapet walls on the north and south side supporting metal trusses. Each parapet wall had a rod that appeared to be designed to tie it back into the center of the building structure. These rods were hidden inside existing walls. Of course these rod locations did not line up with the new wall layout.
The Structural Engineer decided the only way to delete the rods and overcome the truss load problem on the parapet walls was to add a new header inside the 3rd floor along both the north and the south sides of the building. This header would be supported by new columns that could be lined up with the existing beams in locations that were inside the new walls.
Exterior work included new roofs and flashings. All rotted wood fascias, soffits and trim were removed and repaired. The north porch was completely removed and rebuilt, the south porch was shored up and all wood columns removed and replace with new fiberglass columns to match the original ones.
On both porches the metal handrails were completely removed and replaced. All exterior trim work was completed to duplicate and restore the original appearance of this historic building.
On the north side exterior concrete work included new handicapped ramps, sidewalks and new main stairs that lead to the circular patio. On the south side we added a new concrete cap on the porch. This cap adjusted the final height to delete a step at the door way. The cap along with the installation of new sidewalks helped attain ADA compliance on this side of the building.
It was discovered that the south porch was hollow. The existing floor was badly cracked. Since there was no door from this area into the basement it was decided to fill the space using flow fill concrete.
On the north side of the building site work discovered an old stacked stone well. This well was 5 to 6’ in diameter and over 70’ deep. We used over 65CY of Flow fill concrete to fill this area to insure there would be no future problems for the College.
We also discovered that the north wall had settlement cracking. This was seen as vertical cracks along with separation from some of the interior walls. Lafayette College is built on a blue limestone formation and sinkholes are always a concern. To insure that the building had adequate support we added compaction grouting along the north wall. A total of 11.58 CY of grout were injected along this wall.
Exterior masonry repairs included patching and pointing around all four sides of the Building and recreating the corbelled masonry at the two new dormers on the north side.
New concrete retaining walls with brick veneer and cast stone caps were added to the north side creating a garden like appearance with a circular patio. A stone walkway connects the patio with the new stone steps on this side.
Windows in certain areas and the two new dormers were completely removed. These were replaced with Marvin custom window units that were made to fit the existing or new opening. All are clad on the exterior including extruded aluminum trim that was intended to match the original wood trim. All other windows were replaced with Marvin Tilt-Pac windows.
The basement is dedicated mostly to mechanical rooms. There is also a janitor’s closet, a bicycle storage room, a social room and a laundry that occupy this level.
All existing wood floors were jacked up and straightened as much as possible to overcome sagging that occurred throughout the years.
The first floor features a Lobby with a touch screen designed to allow the students to monitor the buildings energy use and see how much gas, water and steam are being used in the building. This floor also includes new men’s and women’s public HC toilets, a HC Accessible Suite and a Library / Study with a 96” flat screen TV.
The second and third floors include (2) Dwelling Units on each floor. Each one is occupied by both men and women in the same area. They share the bathroom and kitchen area along with a common living room. Bedroom areas are designed for single and double occupancies.
Installation of the mechanical systems was extremely difficult due to space limitations of working in an older building. Floor to floor elevation differences did not allow the amount of space needed to run ductwork and other mechanical lines that is normally given in new construction. Creative solutions were worked out between on site Contractors and the Design Team.
The HVAC system includes converting College steam to hot water for heating and a Carrier High Efficiency Unit for air conditioning. Each Dwelling area has fan coil units with individual controls. The control package is by Siemens. This system allows Plant Operations to monitor the building and make adjustments from a remote location. Their ability includes making changes that impact comfort in each room.
There is a new Fire Alarm System, a Burglar Alarm System and a Card Reader Access System. All three are monitored by Campus Department of Public Safety on a 24 hour a day basis.
The building has multiple computer outlets in each room as well as a wireless technology.
Completion of this project was on time and under budget. Miller, Miller and McLachlan have received many compliments on the craftsmanship found in each of the building elements.
Throughout the duration of this project we completed 153 Change Orders that added more than 46 working days to the schedule. We were still able to complete the project in time to move the students in for the fall semester and return $8,605.00 in Cost Savings to the College.
Our Project Manager dedicated over 3,490 hours to the completion of this Project.
The Grossman House is designated as housing for students involved in their Global Studies Program. These are students from other countries or that have completed part of their education overseas.